Introduction
In the world of manufacturing, metal parts play a vital role in various industries, from automotive and aerospace to electronics and construction. These components often require specific surface treatments to improve their performance, durability, and appearance. In this blog, we will delve into the fascinating world of metal part surface treatments, exploring the different techniques, their purposes, and the benefits they bring.
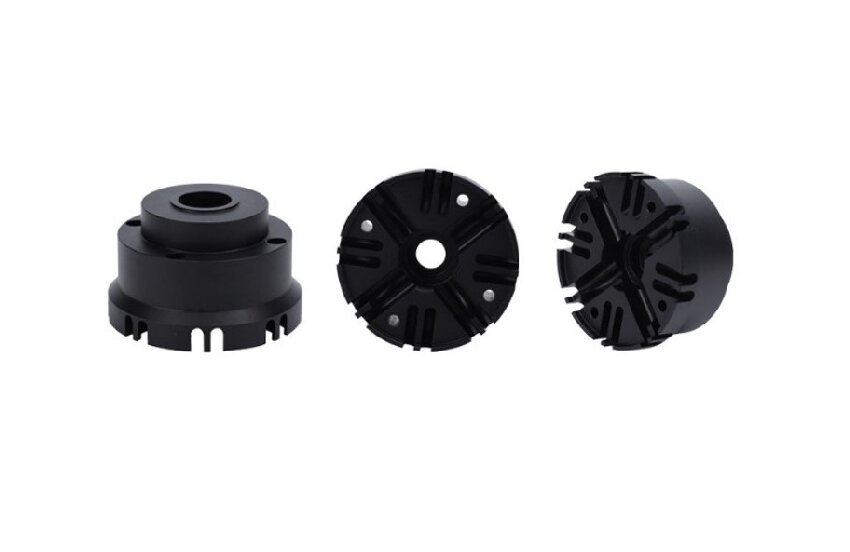
1. Cleaning and Pre-Treatment
Before any surface treatment can be applied, it’s crucial to ensure that the metal parts are clean and free from contaminants like oil, rust, dirt, and scale. Techniques such as degreasing, pickling, and sandblasting are commonly used to prepare the surface for further processing. This step is essential, as it ensures better adhesion of coatings and prevents premature failure of the treatment.
2. Painting and Coating
Painting and coating are among the most common surface treatments for metal parts. They provide a protective barrier against corrosion, wear, and UV radiation. There are several types of coatings, including powder coating, wet paint, and electroplating. Powder coating involves applying a dry, electrostatically charged powder that is then cured under heat, creating a durable finish. Electroplating involves depositing a thin layer of another metal (like zinc or chromium) onto the surface, offering both protection and aesthetic enhancement.
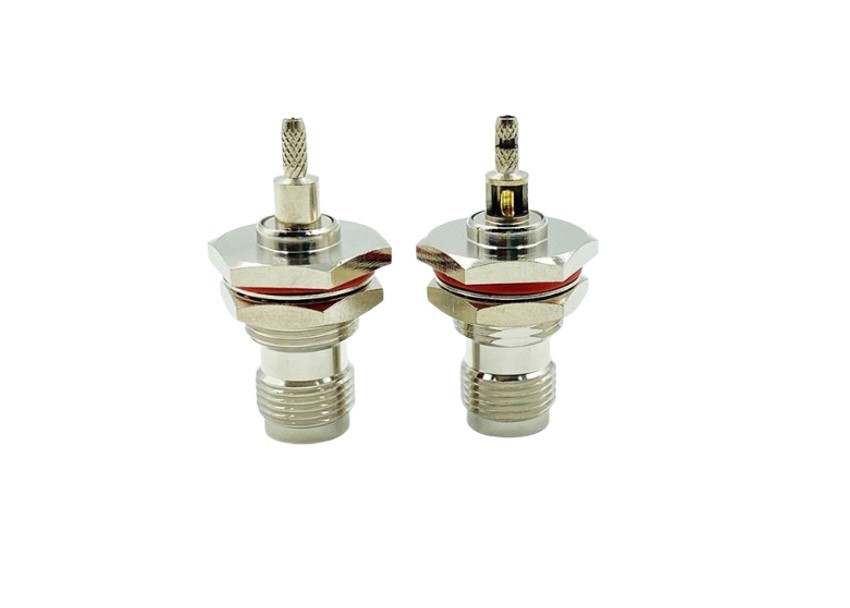
3. Anodizing
Anodizing is an electrochemical process that thickens the natural oxide layer on metals like aluminum, magnesium, and titanium. This treatment improves corrosion resistance, wear resistance, and allows for better adhesion of dyes, making it popular for decorative applications. Anodized metal parts also have excellent electrical insulation properties, making them suitable for electronic components.
Anodizing, an electrochemical process, allows for a wide range of colors on aluminum surfaces. The most common method for coloring anodized aluminum is through dyeing, where the porous anodic layer absorbs dyes. This process can yield a broad spectrum of colors, from classic shades like black, blue, red, green, and yellow to more complex hues and combinations. The actual number of available colors can vary depending on the dyeing techniques, the type of aluminum, and the specific anodizing facility. Some companies offer hundreds of standard colors, and custom colors can also be created upon request. However, it’s important to note that not all colors may be equally resistant to fading or discoloration over time, especially when exposed to sunlight and other environmental factors.
4. Galvanizing
Galvanizing is the process of applying a protective zinc coating to steel or iron to prevent rusting. The most common method is hot-dip galvanizing, where the metal part is immersed in a bath of molten zinc. The resulting zinc coating bonds metallurgically with the base metal, providing a long-lasting barrier against corrosion.

5. Phosphate Conversion Coatings
Phosphate conversion coatings, such as zinc or iron phosphate, are applied to metal surfaces to improve paint adhesion, corrosion resistance, and provide a foundation for other coatings. These coatings are particularly useful in the automotive and military sectors, where high-performance standards are critical.
6. Physical Vapor Deposition (PVD)
PVD is a sophisticated technique used to deposit thin, hard, and wear-resistant films onto metal parts. It involves vaporizing a material in a vacuum and condensing it onto the substrate surface. Common PVD methods include sputtering and evaporation. PVD coatings find extensive use in cutting tools, automotive components, and aerospace applications, where high-temperature and wear resistance are essential.
7. Chemical Vapor Deposition (CVD)
CVD is similar to PVD but involves chemical reactions at high temperatures to form a deposit on the metal part. This process can create ultra-thin, uniform, and adherent coatings, making it ideal for semiconductor devices, aerospace components, and medical implants.
8.Thermal Spray Coatings
Thermal spray coatings involve propelling molten or semi-molten materials onto a surface at high speeds, forming a protective layer. Techniques like plasma spraying, arc spraying, and high-velocity oxy-fuel (HVOF) spraying can create coatings with exceptional bond strength and wear resistance. These coatings are used in industries like power generation, aerospace, and automotive.
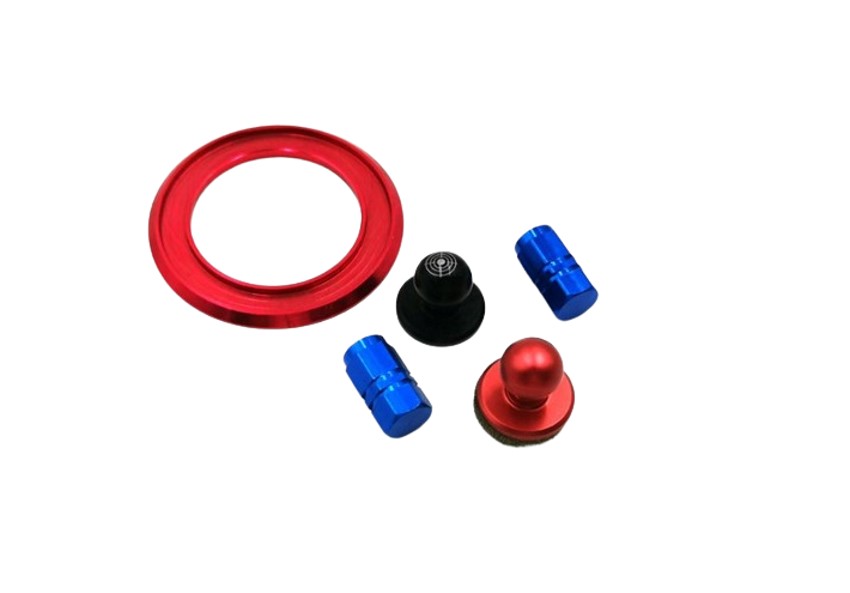
Applications of Surface Treatments in Different Industries
Surface treatments find extensive use across numerous industries due to their wide range of benefits. In the automotive industry, they are applied to engine parts for improved heat management and reduced friction, while in aerospace, corrosion-resistant coatings and surface treatments ensure safety and longevity of aircraft components. The construction sector uses treated metals for architectural features, roofing, and structural elements with enhanced durability and aesthetic appeal. Electrical and electronics industries rely on surface treatments for insulation, conductivity, and component miniaturization. Medical devices often require anti-microbial coatings and corrosion resistance for implantable or surgical instruments. The manufacturing and machinery sectors employ heat treatments and wear-resistant coatings to prolong the life of tools and machinery. Consumer goods, such as appliances and jewelry, benefit from surface treatments for improved appearance and tarnish resistance. These treatments play a vital role in optimizing performance, reliability, and cost-effectiveness across diverse industries.
Factors Influencing the Choice of Surface Treatments
The choice of surface treatment depends on several factors, including the type of material, environmental conditions, mechanical demands, and aesthetic requirements. Material compatibility is crucial, as different treatments work best with specific metals or alloys. Environmental exposure, such as humidity, salt, or chemicals, determines the need for corrosion-resistant coatings. The mechanical demands of the part, like wear resistance or load-bearing capacity, may require heat treatment or hard coatings. Aesthetic considerations, like color, texture, or gloss, influence choices like anodizing, plating, or painting. Economic factors, such as cost and production volume, also play a role in selecting a treatment that balances performance and budget. Regulatory compliance, particularly in industries like medical or aerospace, necessitates treatments meeting strict standards. Additionally, sustainability concerns may drive the choice of eco-friendly or recyclable treatments. Lastly, the desired process efficiency and ease of application can dictate whether to opt for chemical, physical, or electrochemical methods.
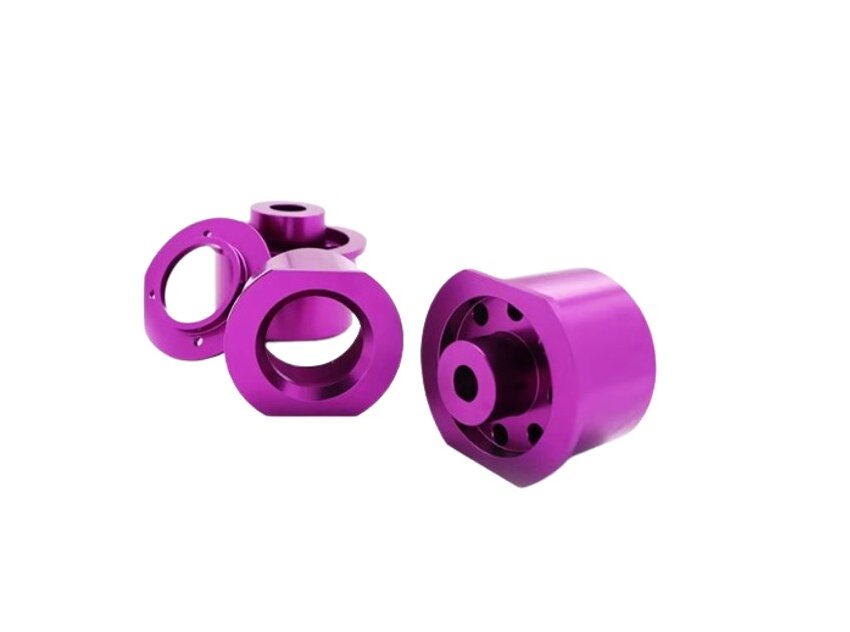
Future Trends in Surface Treatments
The future of surface treatments is likely to be shaped by advancements in technology, sustainability, and Industry 4.0 concepts. Smart coatings, incorporating sensors and self-healing properties, will monitor and maintain surface integrity, reducing maintenance costs and waste. Nanotechnology will enable the creation of ultra-thin, high-performance coatings with tailored properties, such as antimicrobial activity or extreme wear resistance. Environmentally friendly treatments, like bio-based and low-VOC coatings, will gain prominence, adhering to stricter regulations and consumer preferences. Additive manufacturing will influence surface treatments, with processes designed specifically for 3D-printed parts. Machine learning and artificial intelligence will optimize treatment selection and process parameters, ensuring consistency and efficiency. Furthermore, integration with Internet of Things (IoT) will allow real-time monitoring of treatment effectiveness and asset health. These trends promise to revolutionize surface treatments, making them more efficient, sustainable, and adaptable to evolving industrial needs, such as automobile parts, medical parts, equipment parts, motorcycle parts, robot parts, electronic parts and so on.
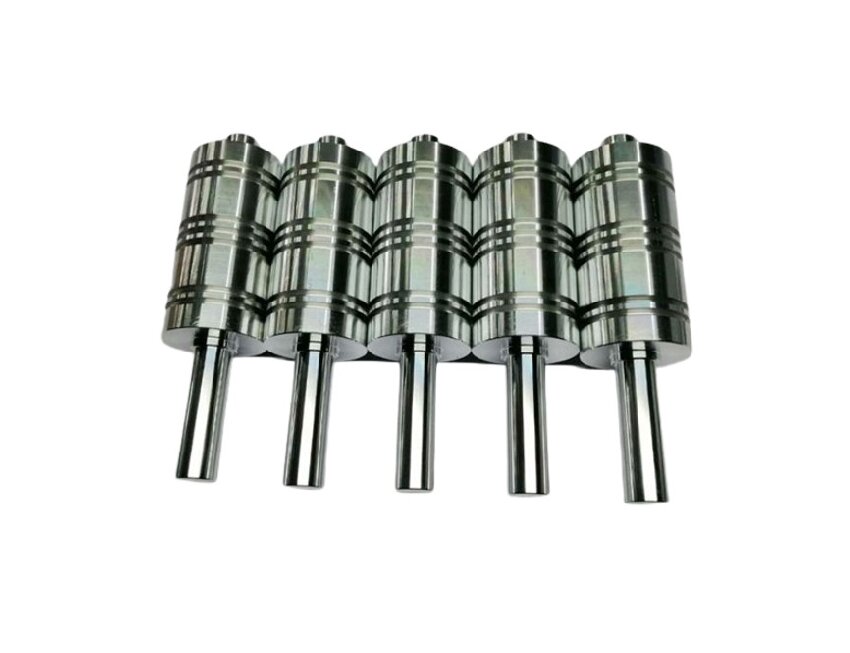
Conclusion
Surface treatments serve to optimize the performance and durability of metal parts by modifying their surface properties. Their primary purpose is to protect against corrosion, enhance wear resistance, and improve aesthetics. These treatments also enable better adhesion for coatings, facilitate heat management, and can introduce special functionalities like electrical insulation or reduced friction. By extending the lifespan of components, they contribute to cost savings and sustainability in various industries. Surface treatments like anodizing and plating protect against environmental degradation, while heat treatment alters the microstructure for increased strength or toughness. Lubrication and PVD coatings enhance mechanical performance, and chemical treatments like phosphating and conversion coatings improve adhesion and corrosion resistance. Overall, surface treatments are crucial for enhancing the efficiency, reliability, and appearance of metal parts in their respective applications.
Surface treatments for metal parts are a testament to the marriage of art and science. Each technique serves a specific purpose, from improving functionality to enhancing aesthetics. As technology advances, we can expect even more innovative and effective surface treatments to emerge, revolutionizing the way we manufacture and utilize metal components. Whether it’s protecting against corrosion, boosting performance, or adding a touch of style, these treatments are indispensable in today’s industrial landscape.