When it comes to manufacturing custom parts, companies often face the challenge of balancing cost and quality. Traditional manufacturing methods like machining and forging are still widely used in many industries, but increasingly, businesses are discovering that custom cast parts can be a more cost-effective solution. As someone who has worked in the casting industry for several years, I’ve seen firsthand how custom castings can offer significant cost savings without compromising quality or performance. In this blog, I’ll break down the reasons why custom cast parts are often the more affordable option compared to traditional manufacturing methods like machining or forging.
1. Lower Upfront Tooling Costs
One of the biggest factors that contribute to the cost-effectiveness of custom cast parts is the relatively low upfront tooling costs. In traditional manufacturing methods, especially machining and forging, creating custom tooling and molds can be a significant investment. For example, machining requires expensive CNC machines, custom fixtures, and tools that need to be fabricated and maintained. Similarly, forging requires specialized dies that are often costly and time-consuming to produce.
In contrast, custom casting typically involves much lower tooling costs. For many casting processes, such as sand casting or investment casting, the molds can be created at a fraction of the cost compared to the tooling required for machining or forging. For instance, in sand casting, the mold is typically made from a mixture of sand, clay, and water, which is not only inexpensive but can be reused multiple times for different parts. This drastically reduces the initial investment, especially for small to medium production runs.
For startups and small businesses, this reduction in tooling costs can be a game-changer. You can create high-quality parts without needing to invest heavily in expensive machinery, making custom casting an accessible option for a wider range of businesses.
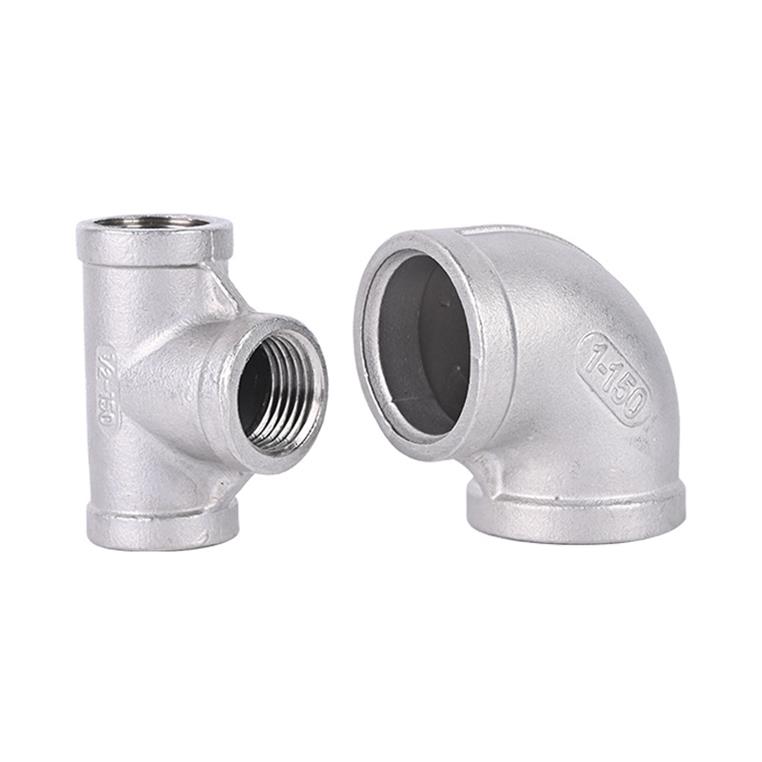
2. Fewer Material Wastes
Another cost benefit of custom casting is that it tends to produce less material waste compared to machining and forging. Machining involves cutting away material from a solid block or billet, often resulting in significant waste. For example, when machining a metal part, a large percentage of the material is often discarded as chips or scraps. In many cases, up to 70% of the initial material can be wasted depending on the complexity of the part and the machining method.
Forging also generates waste, though it’s somewhat less than machining. While forging reshapes a solid piece of metal, some material still has to be trimmed away in post-production. Moreover, the need for high-quality raw materials can further increase costs in forging.
With custom casting, however, the process is designed to create the part directly from the mold. While there’s always some level of waste involved in any manufacturing process, casting is inherently more efficient in its material usage. For instance, precision casting processes like investment casting or die casting can create complex shapes with minimal waste because the molten metal is poured into molds that closely match the desired part shape. This reduction in waste not only saves on material costs but also reduces the environmental impact of manufacturing.
3. Less Labor-Intensive
Labor costs can also be a significant contributor to the overall cost of manufacturing parts. Traditional methods like machining and forging require skilled labor to operate machines, set up tooling, and perform intricate operations on each part. Machining, in particular, is a highly manual process that can take considerable time, especially for complex or tight-tolerance parts. Forging, while less labor-intensive than machining, still requires workers to operate large, specialized equipment and often involves additional steps like trimming and finishing.
Custom casting, on the other hand, is often much less labor-intensive. Once the molds are prepared, the casting process can be automated to a large extent, reducing the need for manual intervention. In many cases, especially with modern casting methods like die casting or sand casting, the mold preparation and pouring process can be done with minimal human labor. Additionally, as casting processes improve, automation and robotics are increasingly being used to further reduce labor costs while maintaining consistent quality.
The lower labor requirements of casting are particularly beneficial for high-volume production runs. Because casting can be highly automated, companies can save on labor costs, even when producing large numbers of parts.
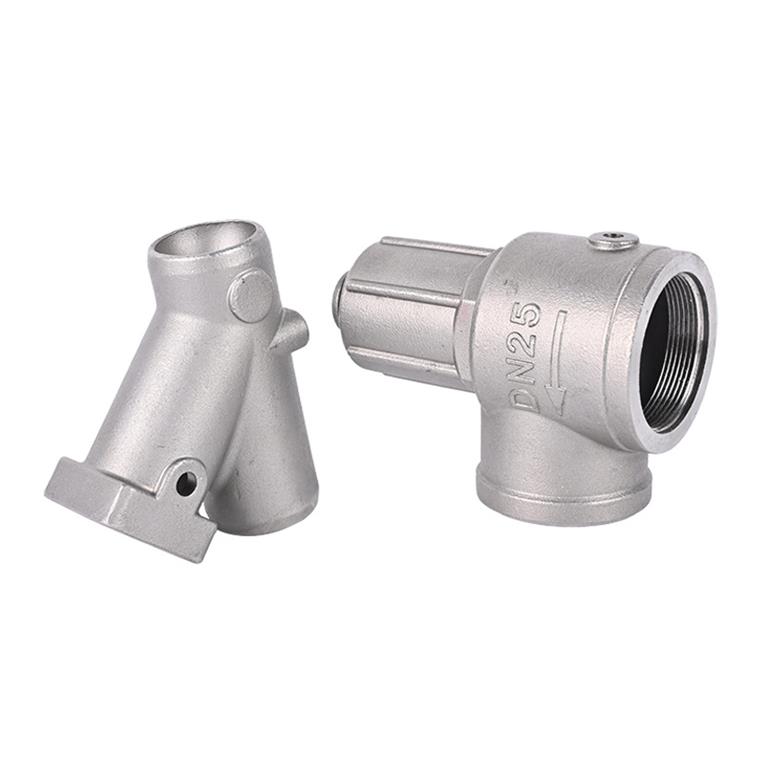
4. Faster Production Times
Time is money in any manufacturing process, and when you’re trying to produce parts quickly to meet customer demands, the speed of production can have a huge impact on costs. Traditional methods like machining often require multiple steps for each part, which can be time-consuming. Even with the most efficient CNC machines, each part may need to be individually set up, run through various processes, and undergo finishing operations like polishing or deburring. These additional steps can significantly slow down production times and increase labor costs.
Similarly, forging can also be a time-intensive process. While forging itself is a fast process, the need for tooling, heat treatment, and post-forging operations like trimming can add considerable time to the overall production cycle.
Casting, however, tends to be much faster for many applications. After the mold is created, the pouring and cooling process can be done relatively quickly, especially with high-pressure die casting or sand casting techniques. The parts produced via casting can often be directly ready for finishing with fewer post-production steps, which speeds up the overall manufacturing timeline. This makes casting an excellent choice for companies that need to produce parts quickly, such as in industries like automotive or consumer goods.
5. Ability to Produce Complex Shapes and Designs
One of the greatest advantages of custom casting is its ability to produce complex shapes and geometries that would be difficult or impossible to achieve with traditional manufacturing methods. Machining, for instance, requires that material be removed from a solid block, so intricate internal features or undercuts are difficult to achieve. Forging is limited in terms of part complexity because it relies on reshaping a single piece of metal, which means creating parts with intricate internal features or detailed surface geometry requires additional steps.
With custom casting, however, you can design parts with a high degree of complexity. Investment casting, for example, is often used to create intricate, detailed parts for industries like aerospace or medical devices, where high precision and complex geometries are essential. Cast parts can also be made with internal voids, thin walls, and complex contours that would be extremely difficult to achieve using machining or forging.
This ability to produce complex shapes means that companies can reduce the need for secondary operations (like machining or welding) to add features, resulting in cost savings and more efficient production.
6. Lower Production Costs for Large Runs
Once the initial setup is complete, casting can be an incredibly cost-effective method for high-volume production runs. While traditional methods like machining may require significant time and effort per part, casting can produce large quantities of parts much more efficiently. After the mold is created, parts can be produced quickly with minimal labor and material waste, and the cost per part decreases significantly as volume increases. This is especially true for casting methods like die casting, which can produce thousands of parts in a single production run.
For companies looking to produce large quantities of parts, casting offers a significant cost advantage over traditional manufacturing methods.
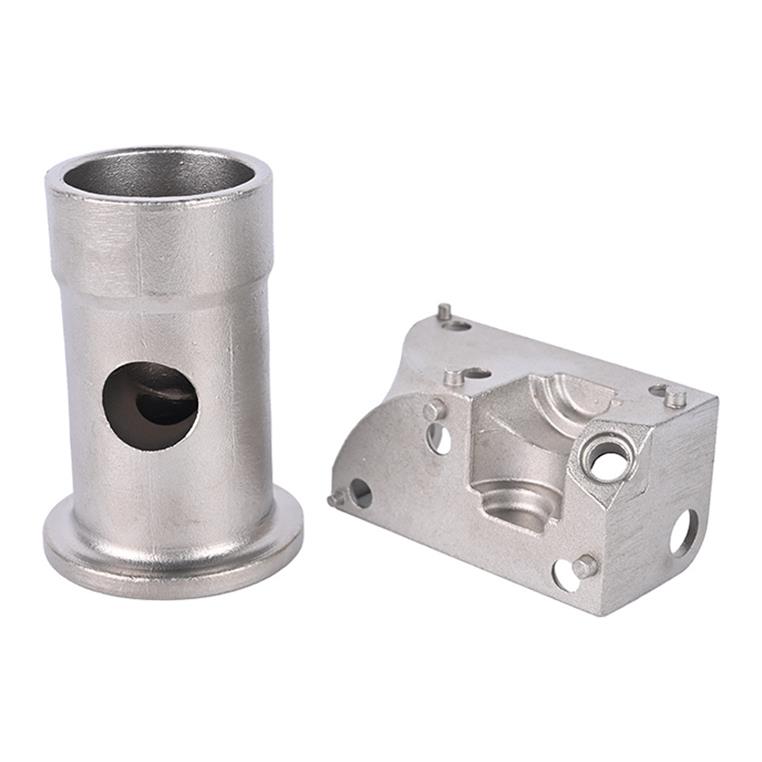
7. Versatility in Material Selection
Custom casting also offers greater versatility in terms of material selection. While machining and forging are often limited to certain types of metal (typically aluminum, steel, or titanium), casting allows you to work with a wider variety of materials, including exotic alloys and specialized metals. This versatility in material selection can provide additional cost savings, especially if a particular alloy is better suited for your application and can help reduce the need for expensive coatings or finishes.
Conclusion
In summary, custom cast parts are often more cost-effective than traditional manufacturing methods like machining or forging due to their lower upfront tooling costs, reduced material waste, lower labor requirements, faster production times, and ability to produce complex shapes. For companies looking to optimize their manufacturing processes, custom casting presents an excellent solution that can deliver high-quality parts at a more affordable price point. By understanding the advantages of custom castings, businesses can make more informed decisions and improve their overall production efficiency.
If you’re considering custom cast parts for your next project, I encourage you to explore the different casting options available and consult with experts in the field. The right casting solution could help you save both time and money while delivering exceptional quality.