When it comes to manufacturing high-quality, durable, and precise metal components, casting plays an essential role in many industries, from automotive to aerospace, construction to machinery. The process of casting parts has been around for centuries, but it continues to be a core method of production due to its versatility and efficiency. In this blog, we’ll explore the basics of casting parts—what casting is, how it works, and the various methods used to produce cast components.
What is Casting?
Casting is a manufacturing process in which a material—typically metal—is heated to a molten state and then poured into a mold to cool and solidify into the desired shape. The mold can be made from a variety of materials, such as sand, metal, or ceramics, depending on the type of casting being used. This method is ideal for creating complex shapes, intricate details, and components with precise tolerances.
The basic concept of casting has remained unchanged over the years: molten material is poured into a mold, and as it cools, it solidifies into the desired form. However, casting techniques have evolved significantly, with new innovations in materials, technology, and equipment enabling greater precision, higher efficiency, and improved quality.
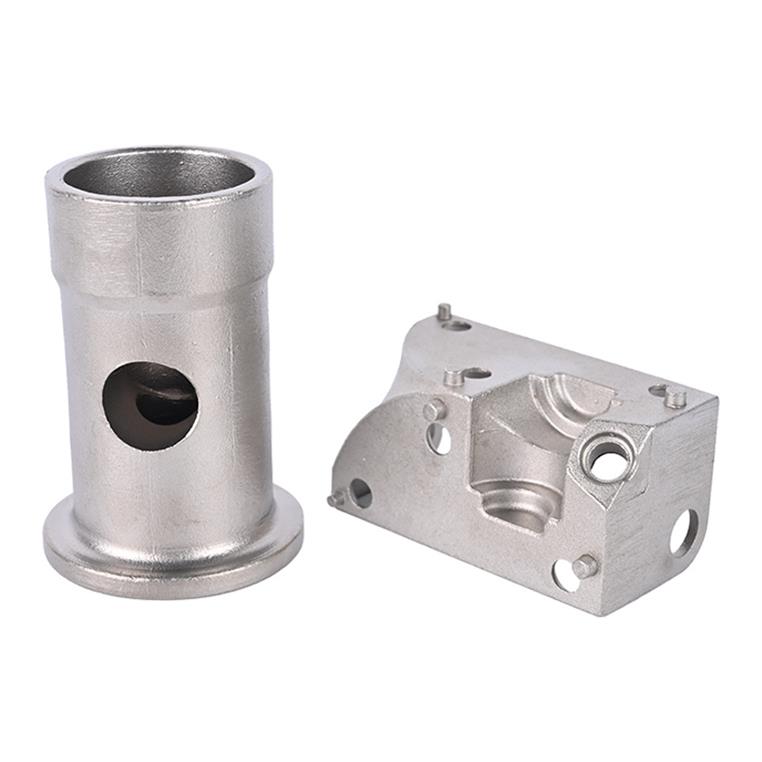
Types of Casting Methods
There are several casting methods, each with its own set of advantages and applications. The most common types of casting methods include:
1. Sand Casting
Sand casting is one of the most traditional and widely used methods of casting. It involves creating a mold out of sand, typically mixed with a binder to give it strength. The mold is then filled with molten metal to form the desired part. Sand casting is popular due to its cost-effectiveness and flexibility—it can be used for a variety of metals, including aluminum, bronze, and iron.
Advantages:
- Low-cost tooling
- High versatility for small to medium-sized production runs
- Capability to cast large and complex parts
Applications: Sand casting is commonly used in industries such as automotive, construction, and heavy machinery, where large, complex metal parts are required.
2. Investment Casting (Lost Wax Casting)
Investment casting, also known as lost wax casting, is a precise casting method that involves creating a detailed mold using a wax pattern. The pattern is coated in a ceramic shell, which is then heated to remove the wax and harden the shell. Once the shell is prepared, molten metal is poured into the mold to create the final part. This process is especially suitable for high-precision components.
Advantages:
- High precision and surface finish
- Ideal for complex shapes and intricate details
- Suitable for a variety of materials, including steel, bronze, and titanium
Applications: Investment casting is commonly used in the aerospace, medical, and jewelry industries, where high precision and quality are essential.
3. Die Casting
Die casting involves forcing molten metal under high pressure into a steel mold, or die. The mold is typically made of two halves that fit together, and the molten metal fills the cavity to form the part. This method is highly effective for producing large volumes of small to medium-sized parts with high dimensional accuracy.
Advantages:
- High production rate
- Excellent surface finish and dimensional accuracy
- Good for thin-walled components
Applications: Die casting is widely used in the automotive, electronics, and consumer goods industries, particularly for producing parts such as engine blocks, housings, and casings.
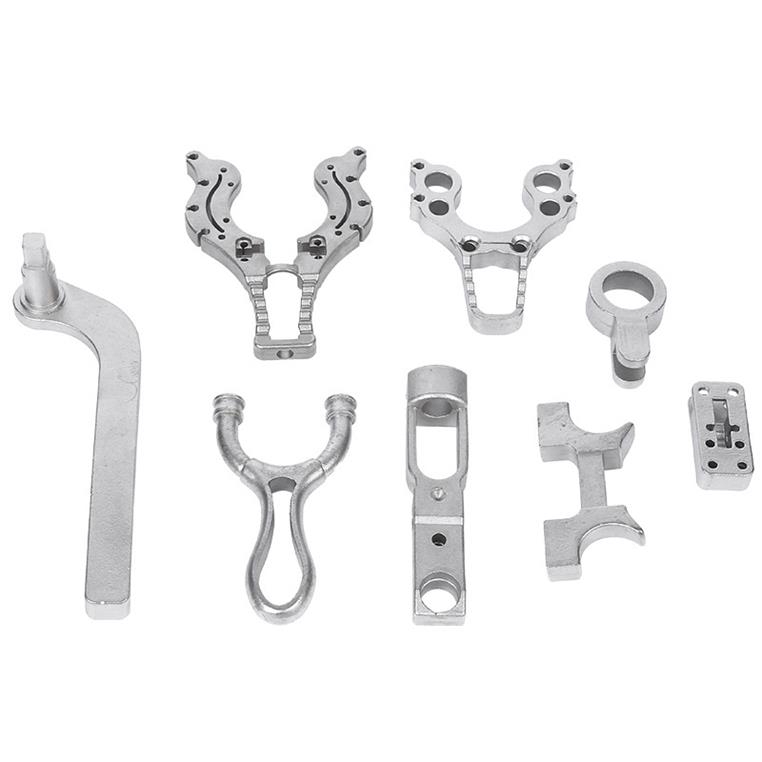
4. Permanent Mold Casting
Permanent mold casting uses molds that are made of metal, typically steel or cast iron, which can be reused multiple times. The mold is preheated before molten metal is poured into it, and the metal solidifies within the mold, creating the part. This method is ideal for medium to high production runs of parts that require a high degree of accuracy and strength.
Advantages:
- High strength and durability of castings
- Suitable for medium to high production runs
- Good surface finish and dimensional accuracy
Applications: Permanent mold casting is often used in the production of parts for the automotive, aerospace, and electrical industries.
5. Shell Mold Casting
Shell mold casting is a variation of investment casting. Instead of using a wax pattern, a pattern is made from a metal or a ceramic material. The pattern is then coated with a thin layer of shell material, which is heated to form the final mold. The molten metal is then poured into the mold to create the part.
Advantages:
- Precision and fine detail
- Ability to produce parts with complex shapes
- Suitable for both ferrous and non-ferrous metals
Applications: Shell mold casting is commonly used in industries requiring high precision, such as aerospace, automotive, and military applications.
Materials Used in Casting Parts
Casting parts can be made from a variety of materials, with metals being the most common. The choice of material depends on the application and desired properties of the final part. Common materials used in casting include:
- Aluminum: Lightweight, corrosion-resistant, and easy to machine, aluminum is often used for automotive and aerospace parts.
- Steel: Strong and durable, steel is commonly used for structural parts in construction, machinery, and automotive applications.
- Iron: Cast iron is known for its excellent castability and wear resistance. It is frequently used in engine blocks, pumps, and other heavy machinery components.
- Bronze and Brass: These copper alloys are known for their excellent corrosion resistance and are often used in marine and plumbing applications.
- Zinc: Zinc is often used in die casting because of its low melting point and good fluidity, making it suitable for complex shapes and thin-walled components.
Advantages of Casting Parts
The casting process offers several advantages, making it an ideal choice for many manufacturing applications:
- Complex Shapes: Casting allows for the production of intricate and complex shapes that may be difficult or expensive to achieve using other manufacturing methods like machining.
- High Precision: Many casting methods, such as investment casting and die casting, offer excellent dimensional accuracy and surface finish, making them suitable for precision parts.
- Material Flexibility: Casting can be performed with a wide range of materials, from metals like aluminum and steel to alloys like bronze and brass.
- Cost-Effectiveness: Casting is often more economical for large production runs of parts, as the molds can be reused many times, and the process is highly automated.
Common Applications of Casting Parts
Casting is used in a variety of industries to produce parts for machinery, transportation, consumer goods, and more. Some common applications include:
- Automotive: Engine blocks, cylinder heads, wheels, and transmission housings are often cast for strength and durability.
- Aerospace: Precision casting is used to create turbine blades, structural components, and other high-performance parts.
- Construction: Cast parts are used in machinery, tools, and building components, such as heavy-duty pumps and valves.
- Electronics: Housing for electrical components, connectors, and casings are often made through die casting.
- Industrial Equipment: Heavy machinery, tools, and equipment often rely on casting to produce durable and precise parts.
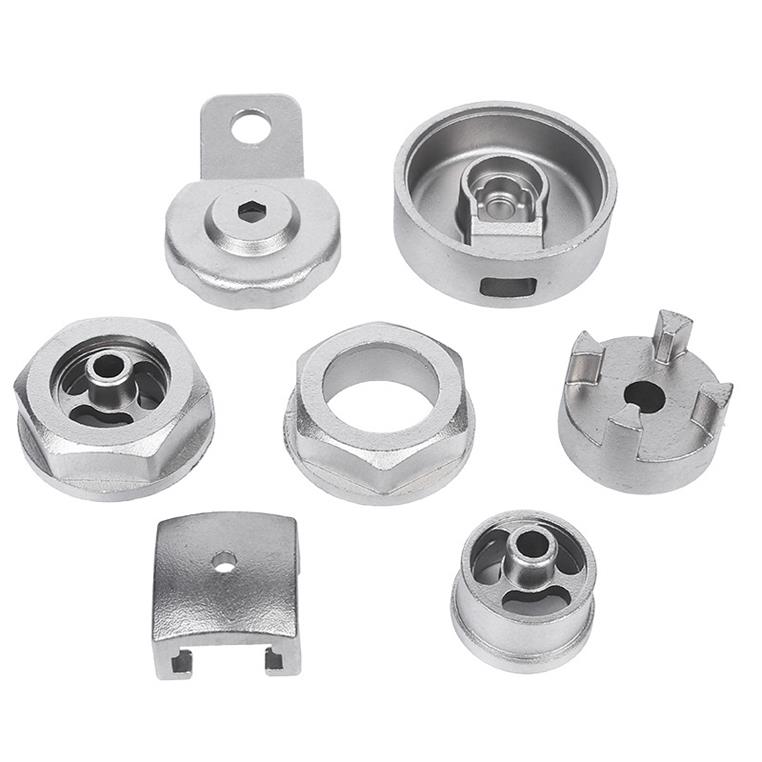
Conclusion
Casting parts is a foundational process in modern manufacturing, offering versatility, cost-effectiveness, and precision. Whether you’re producing small, intricate components or large, complex parts, there’s a casting method suited to your needs. Understanding the different casting techniques and materials available can help you choose the right method for your specific application, ensuring high-quality and reliable parts.
At our company, we specialize in the design, manufacturing, and supply of casting parts tailored to meet your needs. Whether you’re in the automotive, aerospace, or industrial sector, our expertise and cutting-edge technology can deliver exceptional casting solutions that align with your project requirements.
If you’re ready to learn more or start a project, don’t hesitate to contact us. Our team is ready to discuss your casting needs and help you bring your ideas to life!