Milling is an essential process in the manufacturing industry, used to create complex shapes and precise components from a variety of materials. This subtractive manufacturing method involves a rotating cutting tool, known as a milling cutter, that removes material from a workpiece to achieve the desired shape and dimensions. In this detailed guide, we will delve into the world of milling, covering topics such as setup, tool selection, operation, and maintenance to help you master the art of machining parts with accuracy and efficiency.

Understanding Milling Machines
Milling machines come in various types, each suited for different tasks:
- Vertical Milling Machine: The most common type, where the spindle axis is vertically oriented.
- Horizontal Milling Machine: The spindle axis is horizontally oriented, allowing for more complex and heavy-duty milling operations.
- CNC Milling Machine: Computer Numerical Control (CNC) machines automate and precisely control the milling process, offering high accuracy and repeatability.
Essential Tools for Milling
Before diving into milling operations, it’s crucial to familiarize yourself with the essential tools:
- Milling Cutters: These include end mills, face mills, and various specialty cutters tailored for specific materials and operations.
- Workholding Devices: Vises, clamps, and fixtures securely hold the workpiece in place during milling to ensure precision and safety.
- Measuring Instruments: Calipers, micrometers, and depth gauges are indispensable for accurate measurement and quality control.
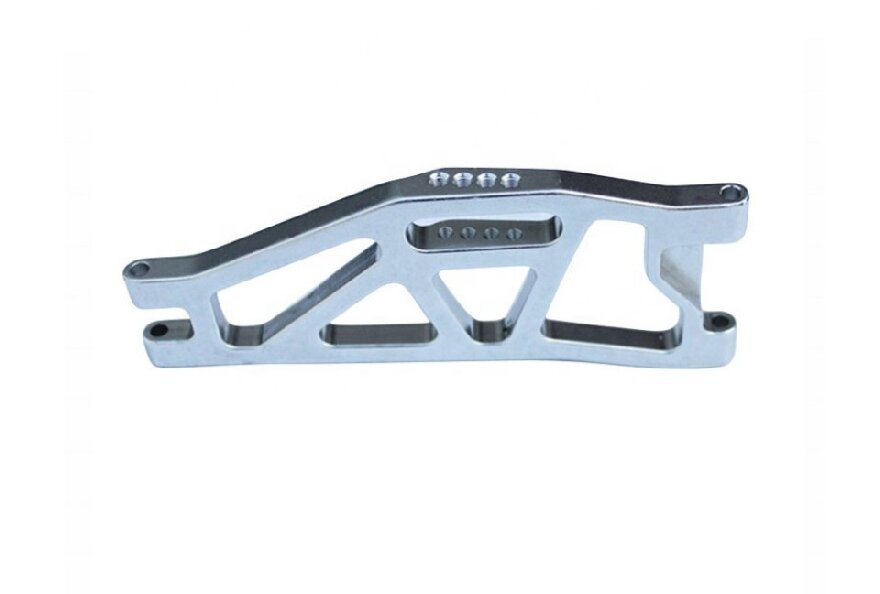
Key Techniques for Milling Success
- Selecting the Right Cutter: Choose a cutter based on: Material: Carbide cutters are ideal for hard materials like stainless steel, while high-speed steel cutters are suitable for softer materials. Operation: Consider the type of cut (e.g., roughing vs. finishing) and the desired surface finish.
- Setting Speeds and Feeds: Optimal speeds (RPM) and feed rates significantly impact machining efficiency and tool life. Refer to cutting speed charts and manufacturer recommendations for best results.
- Understanding Depth of Cut: The depth of cut influences chip thickness and tool wear. Start with conservative depths and increase gradually to maximize material removal rates without compromising tool integrity.
- Securing the Workpiece: Proper workpiece fixation prevents vibrations and ensures dimensional accuracy. Balance clamping force to avoid distortion while maintaining stability throughout the milling process.
Advanced Milling Techniques
- High-Speed Machining (HSM): HSM techniques leverage high spindle speeds and light cuts for enhanced productivity and surface finish. Implement appropriate toolpaths to optimize machining efficiency.
- Trochoidal Milling: This method involves milling in a continuous curve, reducing tool wear and improving chip evacuation in difficult-to-machine materials.
- Climb vs. Conventional Milling: Choose between climb and conventional milling based on tool engagement and workpiece material to minimize tool deflection and achieve superior surface finish.
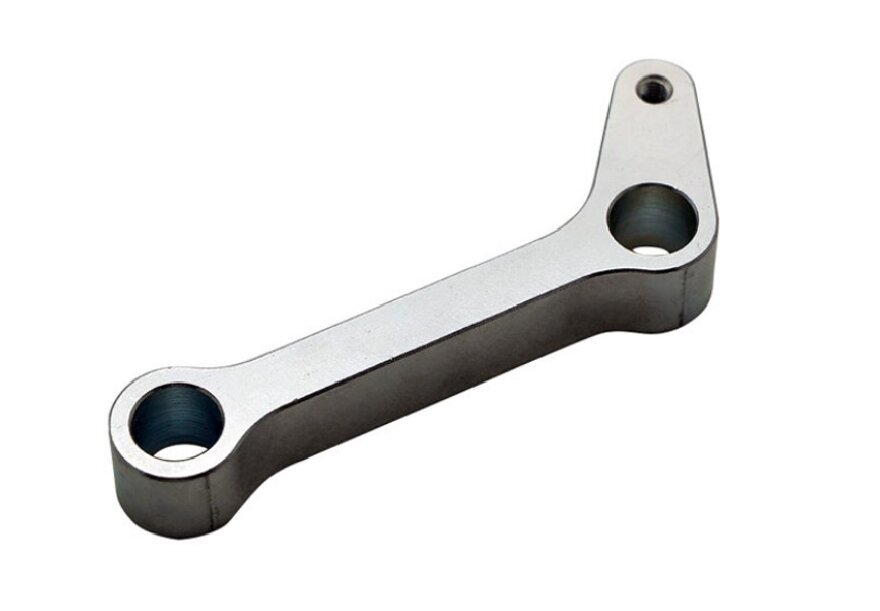
Tips for Optimal Results
- Tool Maintenance: Regularly inspect and maintain milling tools to ensure sharpness and performance.
- Coolant and Lubrication: Use coolant to dissipate heat and prolong tool life, particularly in high-speed and heavy-duty milling operations.
- Quality Control: Verify dimensions and tolerances throughout the machining process to meet design specifications and customer requirements.
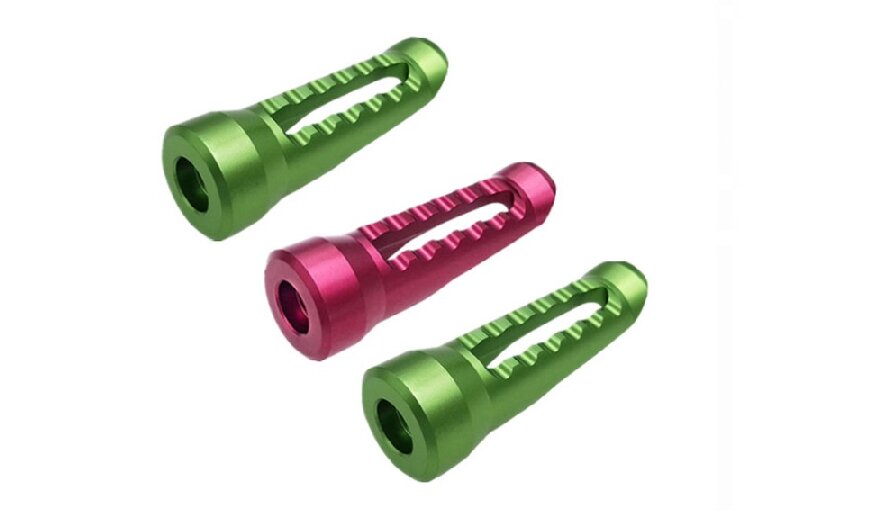
CNC milling machined parts type
- Simple Parts: These include basic components like brackets, plates, blocks, and bolts. They typically have straightforward geometries with holes, slots, and flat surfaces.
- Complex Parts: These parts have intricate geometries, such as gears, splines, automobile parts, motorcycle parts, dovetail slides, and contoured surfaces. They often require multiple axes of motion for machining.
- Functional Parts: These are components that serve specific functions in machines or devices, such as bearings, bushings, shafts, and connectors. They may have tight tolerances and require specialized finishes.
- Prototype Parts: In the product development process, CNC milling is often used to create prototypes to test form, fit, and function before mass production. These parts can range from simple to complex designs.
- Aerospace Parts: CNC milling is extensively used in the aerospace industry to manufacture high-precision parts, including engine components, airframe structures, and control surfaces. These parts often require exotic materials like titanium and aluminum alloys.
- Medical Devices: CNC-milled medical parts include implants, surgical instruments, and dental prosthetics. They need to meet strict standards for biocompatibility, precision, and surface finish.
- Electronics Enclosures: CNC milling can create custom housings and enclosures for electronic devices, with features like cooling vents, threaded holes, and precise mating surfaces.
- Artistic and Ornamental Parts: CNC milling can also be used to create intricate designs on sculptures, signs, and decorative items, allowing for detailed replication and customization.
- Jigs and Fixtures Parts: These are tools used to hold, support, or position workpieces during machining or assembly processes. They are often CNC-milled for accuracy and repeatability.
- Molds and Dies: CNC milling is employed to create molds and dies for injection molding, casting, and stamping processes. These tools can be highly complex and require precision machining.

CNC milling machinable materials
CNC milling machines can handle a broad array of materials, including metals like aluminum, steel, titanium, copper, and brass; plastics such as ABS, polycarbonate, polyetherimide, and POM; composites like carbon fiber and glass fiber reinforced polymers; wood and wood derivatives; ceramics and glasses; and even graphite and stone. Material selection depends on factors like strength, durability, weight, cost, and finish requirements. Each material requires tailored cutting tools, speeds, and feeds for optimal machining performance. For instance, metals often require carbide tools, while plastics may use high-speed steel or coated carbide. Composites and woods can be machined with specialized cutters designed to handle fibers. Ceramics and glasses demand diamond or tungsten carbide tools due to their hardness.

Conclusion
Milling is a versatile and powerful manufacturing technique that requires careful planning, tool selection, and execution to produce high-quality parts. By understanding the basics of milling machines, workholding, tool geometry, cutting parameters, and safety precautions, you can elevate your skills and produce intricate components with precision and efficiency. Remember, continuous learning and practice are key to mastering the art of milling.