In the world of manufacturing and engineering, turning is a fundamental process used to shape materials into precise components. Whether you’re crafting a high-performance automotive part or a delicate aerospace component, understanding the nuances of turning can significantly impact your project’s success. In this guide, we’ll delve into the essentials of turning, exploring everything from the basic concepts to advanced techniques, ensuring that you have the knowledge to tackle your next machining challenge with confidence.
What is Turning?
Turning is a machining process where a cutting tool removes material from a rotating workpiece. This rotation, combined with the tool’s movement, creates a cylindrical shape. Typically performed on a lathe, turning is ideal for creating parts with symmetrical, round shapes, such as shafts, pins, and bushings. The process is versatile and can be used on various materials, including metals, plastics, and composites.
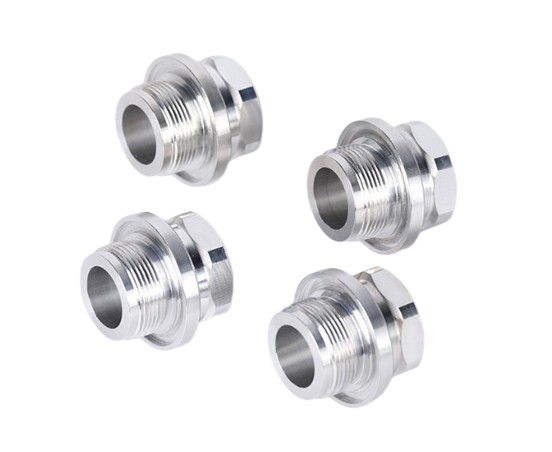
Key Components of a Turning Operation
- Lathe Machine: The heart of any turning operation. Modern lathes come in various configurations, including manual, CNC (Computer Numerical Control), and automatic lathes. Each type offers different levels of precision and automation.
- Workpiece: The material being turned. It’s usually held in place by a chuck or collet. The material’s properties, such as hardness and ductility, will influence the turning parameters.
- Cutting Tool: The implement used to remove material from the workpiece. Cutting tools can be made from various materials, including high-speed steel (HSS), carbide, and ceramics. The choice of tool depends on the material being machined and the desired finish.
- Tool Post: The component that holds and positions the cutting tool relative to the workpiece. It’s crucial for precise control of the cutting process.
- Tailstock: A component that supports the opposite end of the workpiece, providing stability and reducing vibrations.
Turning Process Overview
The turning process involves several key steps:
- Setup: Position the workpiece in the lathe’s chuck or collet, ensuring it’s securely clamped. Adjust the tailstock if necessary for support.
- Tool Selection: Choose the appropriate cutting tool based on the material and desired finish. Install the tool in the tool post and adjust its position.
- Cutting Parameters: Set the lathe’s speed, feed rate, and depth of cut. These parameters vary depending on the material and the tool used.
- Turning: Engage the lathe and begin the turning operation. Monitor the process closely to ensure proper material removal and prevent defects.
- Finishing: After the rough turning is complete, perform finishing cuts to achieve the desired surface finish and dimensional accuracy.
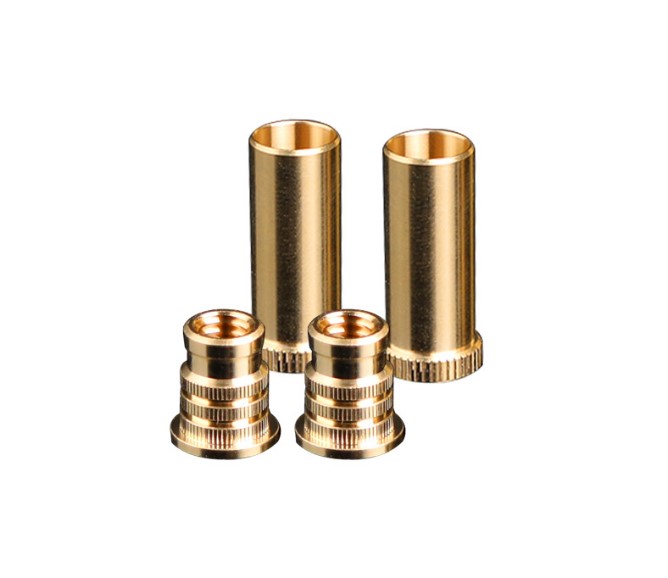
Turning Techniques
- Rough Turning: This is the initial stage where most of the material is removed. The primary goal is to bring the workpiece close to the final dimensions.
- Finish Turning: After rough turning, finish turning is used to refine the surface and achieve the precise dimensions and smooth surface finish required for the final part.
- Facing: This involves cutting a flat surface perpendicular to the axis of rotation. It’s often the first operation performed on a workpiece to create a reference surface.
- Parting Off: This technique involves cutting the workpiece into separate sections. It’s commonly used to remove finished parts from the remaining material.
- Grooving: Creating grooves or recesses in the workpiece, often used for creating features like O-ring grooves or keyways.
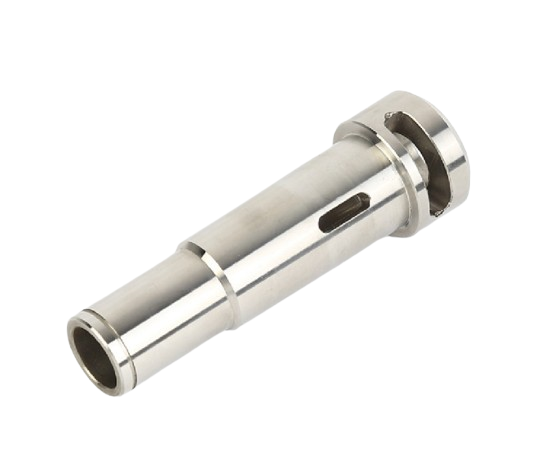
Advanced Turning Techniques
- CNC Turning: Computer Numerical Control (CNC) lathes automate the turning process, allowing for complex shapes and higher precision. CNC lathes use programmed instructions to control the cutting tools and workpiece movement, reducing the potential for human error.
- Live Tooling: In CNC lathes, live tooling allows for additional operations, such as drilling and milling, to be performed simultaneously with turning. This reduces the need for multiple setups and increases productivity.
- Boring: This technique involves enlarging existing holes or cavities in the workpiece. It’s used to achieve precise internal diameters and improve surface finish.
- Thread Cutting: Creating threads on the workpiece, either external or internal. This can be done using dedicated threading tools or through CNC programming.
Material Considerations
The choice of material significantly impacts the turning process:
- Metals: Materials like aluminum, steel, and titanium are common in turning. Each metal has different cutting requirements, such as speed and feed rates.
- Plastics: Plastics are often used for their lightweight and corrosion-resistant properties. They typically require different cutting tools and parameters compared to metals.
- Composites: Composite materials, such as carbon fiber, require specialized cutting tools and techniques to prevent damage and ensure accurate machining.
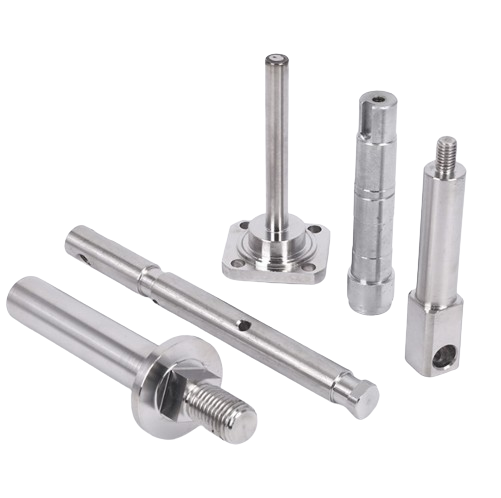
Safety Considerations
Turning operations involve high-speed rotating parts and sharp cutting tools, making safety a priority:
- Personal Protective Equipment (PPE): Always wear safety glasses, gloves, and hearing protection.
- Machine Maintenance: Regularly inspect and maintain the lathe to ensure it’s in good working condition.
- Proper Training: Ensure that anyone operating the lathe is adequately trained and familiar with its controls and safety procedures.
- Workpiece Inspection: Regularly check the workpiece during machining to prevent potential issues such as tool wear or material defects.
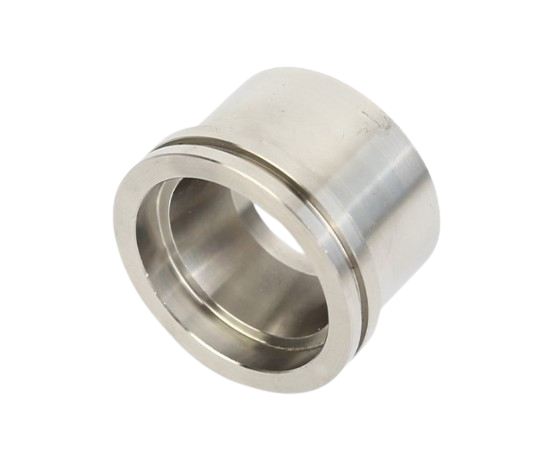
Key Applications of Turning Parts:
- Automotive Industry: Engine Components: Cylinders, pistons, crankshafts, and camshafts are often turned to achieve precise tolerances necessary for engine efficiency. Transmission Parts: Gears, shafts, and bearings require precise dimensions to ensure smooth operation and durability. Braking Systems: Brake discs and rotors need to be precisely turned to maintain safety and performance standards.
- Aerospace Manufacturing: Airframe Components: Precision turning is essential for creating lightweight yet strong components like wing struts and fuselage parts. Engine Parts: Turbine blades, engine mounts, and compressor wheels require high-precision turning to withstand extreme conditions. Avionics Hardware: Connectors, switches, and other small components benefit from the precision offered by turning processes.
- Medical Devices: Surgical Instruments: Needles, drills, and other tools require precise turning to ensure safe and effective use during surgeries. Prosthetics: Custom-fit prosthetic limbs and components are often turned to match individual patient needs. Dental Equipment: High-speed dental drills and other precision instruments benefit from the accuracy of turning processes.
- Consumer Goods: Household Appliances: Components like fan blades, gears, and motor shafts in kitchen appliances and HVAC systems are typically turned. Electronics: Precision turning is used for parts in smartphones, laptops, and other electronic devices, including connectors and casing components. Sports Equipment: Golf club heads, bicycle components, and other sports equipment benefit from the strength and precision provided by turning processes.
- Energy Sector: Renewable Energy: Wind turbine blades, solar panel mounting hardware, and components for hydroelectric generators often require precision turning. Oil and Gas**: Valves, pipes, and fittings must be accurately turned to ensure reliability and safety in harsh environments. Nuclear Power: Precision turning is crucial for components in nuclear reactors and related systems.
- General Manufacturing: Machinery Components: Shafts, gears, and bearings used in heavy machinery and industrial equipment are typically turned. Plumbing Fixtures: Faucets, valves, and other plumbing components often require turning to ensure proper fit and function. Furniture Hardware: Screws, bolts, and decorative elements in furniture benefit from the precision of turning processes.
The applications of turning parts span across numerous industries, showcasing their importance in manufacturing. Their ability to produce components with high accuracy and repeatability makes them an essential part of the modern industrial landscape. As technology advances, the demand for precision turning continues to grow, driving innovation and efficiency in manufacturing processes worldwide.
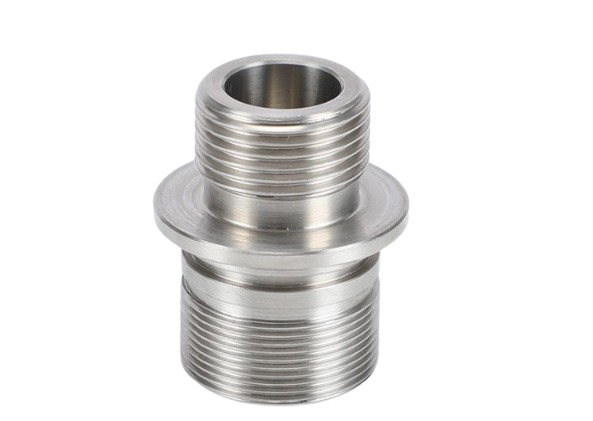
Conclusion
Turning is a versatile and essential machining process that requires a blend of skill, knowledge, and precision. By understanding the key components, techniques, and considerations involved, you can enhance your turning operations and achieve high-quality results. Whether you’re working with metals, plastics, or composites, mastering the art of turning will empower you to tackle a wide range of manufacturing challenges with confidence.
Turning parts are essential in ensuring the efficiency and durability of modern technologies. Their applications span across various industries, making them a fundamental component of global manufacturing processes.