When it comes to custom castings, choosing the right material can be the difference between a high-performing part and one that doesn’t meet your expectations or requirements. Having worked in the casting industry for years, I’ve seen firsthand how important it is to make an informed decision about material selection. After all, materials dictate not only the performance and durability of the final product but also its cost, manufacturability, and ability to withstand specific environmental conditions.
In this blog, I’m going to walk you through how to select the right material for your custom casting needs. We’ll cover the key factors to consider, the different types of materials available, and how to balance application requirements with your budget. Whether you’re designing parts for automotive, aerospace, industrial machinery, or any other field, this guide will help you make a more informed decision when choosing materials for custom cast parts.
1. Understand the Key Factors for Material Selection
Before diving into the specifics of material types, it’s essential to understand the key factors that should influence your decision when selecting materials for custom castings:
a. Mechanical Properties
The mechanical properties of a material—such as strength, hardness, toughness, and fatigue resistance—are crucial to ensuring that your part can withstand the operating conditions it will face. For example, parts that will be subjected to high loads or stresses (like those in automotive or aerospace applications) must be made from materials that can handle these forces without failing. On the other hand, materials for decorative parts may prioritize appearance over strength.
b. Corrosion Resistance
Depending on the environment in which the part will be used, corrosion resistance may be a critical factor. For instance, marine components or parts exposed to harsh chemicals need to be made from materials that can resist rust, oxidation, or other forms of degradation.
c. Thermal Properties
Some applications require cast parts to withstand extreme temperatures. In these cases, materials with high thermal conductivity, low thermal expansion, or resistance to heat (such as heat-resistant alloys) are required. Examples of industries where thermal properties are essential include aerospace and power generation.
d. Cost
Of course, budget is a huge factor when selecting materials for custom castings. While high-performance materials like titanium or special alloys offer exceptional properties, they can also be significantly more expensive. Finding the right balance between performance and cost is key.
e. Workability
The material should also be easy to cast into the desired shape. Some metals are easier to cast than others, and some might require more complex processes, adding to the overall cost. For example, aluminum and copper alloys are generally easier to cast compared to materials like stainless steel, which might need more complex techniques.
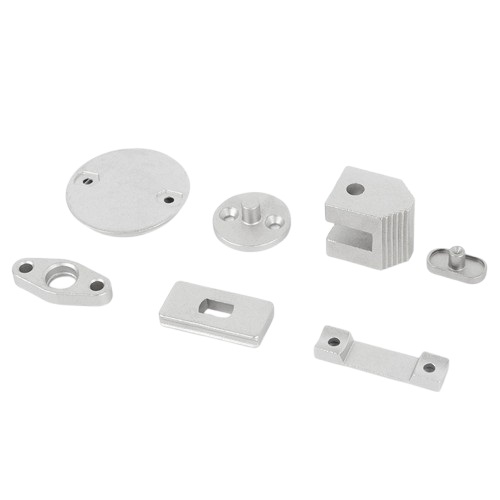
2. Types of Materials for Custom CastingsMaterials for Custom Castings
There are various types of materials commonly used in custom casting. Each material type has its own unique set of advantages and disadvantages depending on the application. Let’s explore the most common materials and their best use cases:
a. Aluminum Alloys
Aluminum is one of the most popular materials for custom castings, especially in industries like automotive, aerospace, and electronics. The main reason for aluminum’s popularity is its combination of light weight, excellent corrosion resistance, and good strength-to-weight ratio.
- Best Applications: Aluminum castings are used extensively in the automotive industry (e.g., engine blocks, transmission housings, wheels), aerospace (e.g., structural components, engine parts), and consumer products (e.g., housings for electronics).
- Benefits: Lightweight, good thermal and electrical conductivity, high corrosion resistance, relatively low cost.
- Drawbacks: While aluminum has great strength, it may not be suitable for parts that need to withstand extreme stress or high temperatures.
b. Steel Alloys
Steel alloys, including carbon steel and stainless steel, are also common choices for custom castings. Steel is known for its strength, durability, and versatility, making it suitable for a wide range of applications.
- Best Applications: Steel castings are used in heavy machinery, automotive components (e.g., chassis parts, engine components), and tools (e.g., gears, dies).
- Benefits: Excellent strength, toughness, and wear resistance. Stainless steel is highly corrosion-resistant.
- Drawbacks: Heavier than aluminum, and can be more expensive due to the need for specialized alloys or heat treatments.
c. Cast Iron
Cast iron is one of the oldest and most widely used materials for casting. It is known for its excellent castability, high wear resistance, and vibration damping properties.
- Best Applications: Cast iron is often used in the automotive industry (e.g., engine blocks, brake rotors), industrial machinery (e.g., housings, frames), and construction equipment.
- Benefits: Good machinability, high wear resistance, good castability, and low cost.
- Drawbacks: Brittle compared to steel, meaning it can fracture under impact or high stress.
d. Copper Alloys (Bronze and Brass)
Copper alloys, including bronze and brass, are known for their excellent corrosion resistance, good electrical and thermal conductivity, and attractive appearance. They are often used for parts that require resistance to oxidation, corrosion, or wear.
- Best Applications: Copper alloys are commonly used in marine components, electrical connectors, pumps, valves, and decorative items.
- Benefits: Excellent corrosion resistance (especially in marine environments), high conductivity, aesthetic appeal.
- Drawbacks: Can be more expensive than aluminum or cast iron and may not provide the same strength-to-weight ratio.
e. Nickel Alloys
Nickel alloys, particularly those used in investment casting, are known for their high-temperature resistance, making them ideal for extreme applications like aerospace, power generation, and chemical processing.
- Best Applications: High-performance aerospace components (e.g., turbine blades), chemical equipment, and high-temperature power generation components.
- Benefits: Exceptional strength and performance at high temperatures, excellent corrosion resistance.
- Drawbacks: High cost, more difficult to cast than other metals.
f. Titanium Alloys
Titanium is a lightweight, strong, and highly corrosion-resistant material. However, it is one of the most expensive metals to use for casting. As a result, it’s typically reserved for high-performance applications.
- Best Applications: Aerospace, medical implants, high-performance automotive applications (e.g., suspension components, exhaust systems).
- Benefits: High strength-to-weight ratio, excellent corrosion resistance, ideal for high-performance applications.
- Drawbacks: Expensive, harder to work with compared to other materials like aluminum.
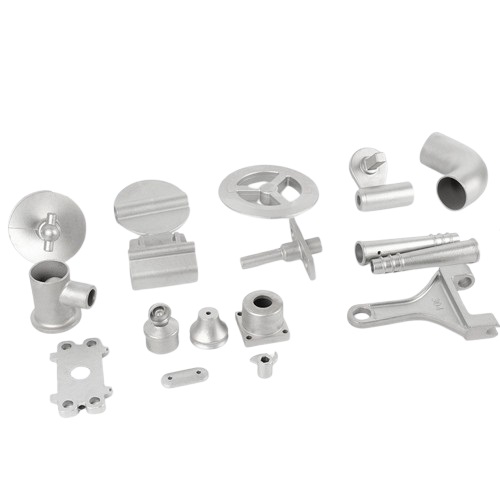
3. How to Choose the Best Material Based on Application and Budget
a. Match Material Properties to the Application
The most important step in choosing the best material for your casting is to match its properties with the requirements of your application. For example:
- If you need a part that can withstand high temperatures and stresses, you’ll likely need a material like steel, nickel alloy, or titanium.
- If weight reduction is a priority, aluminum is a great choice due to its low density.
- If corrosion resistance is critical (like in marine environments), then materials like stainless steel, bronze, or brass should be considered.
b. Consider Production Volume and Complexity
Material costs can vary significantly depending on the production volume and the complexity of the part. For low-to-medium-volume production runs, materials like aluminum or cast iron are usually cost-effective. For high-volume production, you may need to balance cost with material properties and choose a more affordable alloy without compromising performance.
c. Balancing Budget and Performance
If your budget is a bit tight, it’s important to find the best material that balances performance with cost. While high-performance materials like titanium and nickel alloys offer superior properties, they are often out of reach for many projects due to their high cost. In this case, materials like aluminum alloys or steel might be suitable alternatives that still provide a high level of performance at a fraction of the cost.
d. Material Availability and Lead Time
Some materials may have longer lead times or be harder to source depending on the casting process and the complexity of the part. It’s important to consider not only the material cost but also the lead time when making your selection, especially if you’re working on a tight deadline.
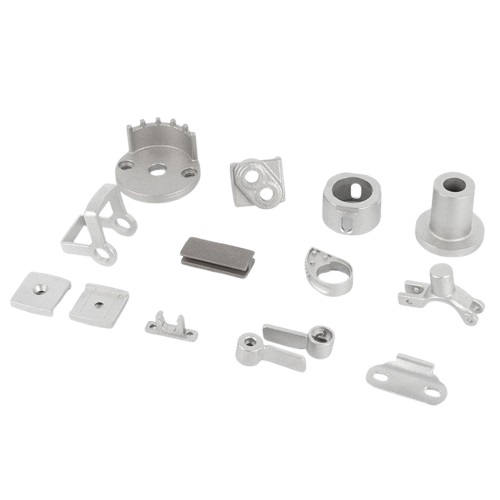
4. Conclusion
Choosing the right material for custom castings is a critical decision that directly impacts both the performance of your part and the overall cost of production. By considering factors like mechanical properties, corrosion resistance, thermal performance, budget, and manufacturability, you can make an informed choice that meets the needs of your application.
Having worked on numerous projects across different industries, I can confidently say that there is no one-size-fits-all solution when it comes to material selection. Every project has unique requirements, and the best material for your custom cast part will depend on your specific needs, goals, and budget.
If you’re unsure which material is right for your casting, working with experienced casting engineers or a reputable foundry can provide valuable insights and help you make the best decision. They can guide you through the process, suggest suitable materials, and ensure that your custom cast parts are produced to the highest standards.