When it comes to manufacturing custom parts, one of the most versatile and cost-effective solutions is custom casting. Over the years, I’ve had the privilege of working with clients across a wide variety of industries, and time and time again, I’ve seen how custom cast parts are essential for producing high-quality, durable, and cost-efficient components. From automotive to aerospace to manufacturing, custom casting plays a crucial role in the production of parts that are integral to the functioning of complex systems and products.
In this post, I’ll take you through some of the key industries that benefit from custom cast parts, and explain why casting is often the preferred choice for producing high-performance, intricate components.
1. Automotive Industry: Precision, Durability, and Cost-Efficiency
The automotive industry is one of the largest users of custom cast parts, and for good reason. Custom castings help automakers create components that are not only lightweight but also durable and cost-effective. I’ve seen firsthand how custom casting enables automotive manufacturers to meet the exacting standards for strength, precision, and performance that the industry demands.
Lightweight and Strong Parts
One of the most important factors in the automotive industry today is weight reduction, particularly with the push toward electric vehicles (EVs). Custom cast parts, such as aluminum engine blocks, transmission cases, and suspension components, are often significantly lighter than their forged or machined counterparts. This weight reduction directly contributes to improved fuel efficiency and performance—critical factors for both traditional gasoline vehicles and electric vehicles.
By using custom casting, automakers can produce parts with intricate designs and reduced weight without compromising strength. For example, die-cast aluminum parts are widely used for various engine components, where strength and lightweight properties are essential. These cast parts also provide excellent thermal conductivity, which is crucial for engine performance.
Complex Geometries
Another area where custom casting shines in the automotive sector is its ability to produce complex shapes. For parts such as intake manifolds, turbochargers, or even decorative trim, casting allows for the creation of intricate designs that would be difficult or expensive to achieve with machining. The ability to produce these complex parts in a single piece (instead of welding multiple parts together) helps to improve both production speed and reliability.
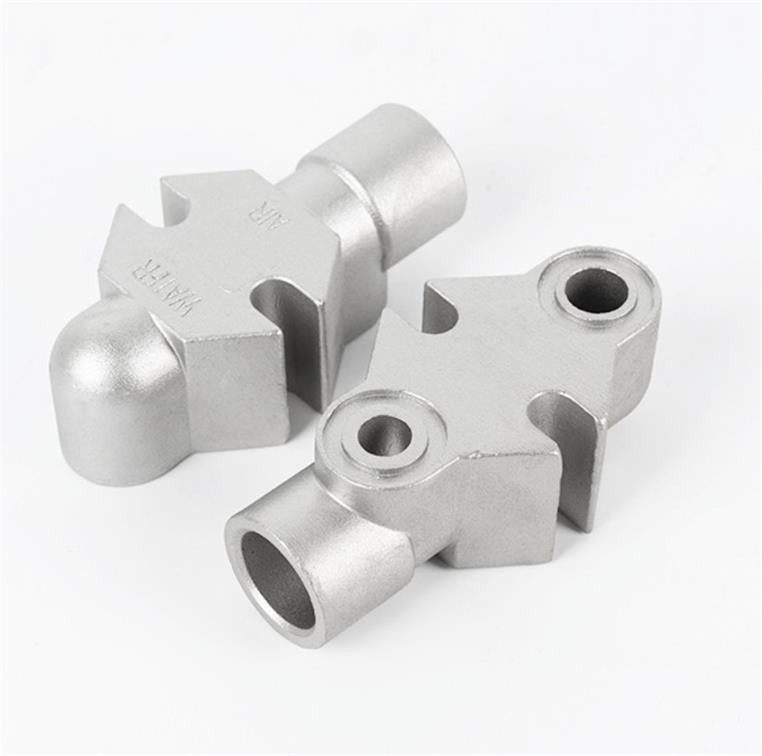
2. Aerospace Industry: Precision and Performance Under Extreme Conditions
The aerospace industry is another sector that heavily relies on custom cast parts. When it comes to aerospace components, precision, performance, and reliability are not just desirable—they are critical. Custom castings are essential in the creation of parts that must withstand extreme temperatures, high stress, and demanding operational conditions.
Strength-to-Weight Ratio
Just like in the automotive industry, the aerospace sector places a high priority on reducing weight. Aerospace components, including turbine blades, engine casings, and landing gear components, must be lightweight yet incredibly strong. Custom casting, especially techniques like investment casting, provides the ability to produce high-strength components with minimal material usage. The casting process allows for more complex internal geometries, such as cooling channels in turbine blades, which improves the efficiency and durability of the component.
In aerospace, aluminum and titanium alloys are often used for casting, as these materials offer a favorable strength-to-weight ratio. Cast titanium, for instance, is a popular material for aerospace applications due to its excellent resistance to heat and corrosion, making it ideal for parts that are subjected to high temperatures and extreme environments.
High Precision and Tolerances
Aerospace components require exceptional precision, often within thousandths of an inch. Custom casting allows manufacturers to meet these stringent requirements. Investment casting, in particular, is ideal for producing complex parts with tight tolerances. This process involves creating a wax pattern of the part, coating it in a ceramic shell, and then melting out the wax to create the mold. The result is a high-precision part with an excellent surface finish, which is essential in aerospace applications where even the smallest flaw could have catastrophic consequences.
Custom cast parts are used for a variety of critical applications in aerospace, including engine components, airframe parts, and structural elements of aircraft. These parts must meet demanding performance standards to ensure safety and reliability, making casting an indispensable technique for this sector.
3. Manufacturing Industry: Versatility and Cost Savings
The manufacturing industry is vast and encompasses everything from heavy machinery to consumer electronics, and custom casting plays a pivotal role in producing high-quality parts for a wide range of products. I’ve worked with manufacturers in countless sub-sectors, and one of the common themes is the versatility and efficiency that casting brings to the table.
Cost-Effective Production of Complex Parts
In many cases, the manufacturing industry requires custom parts with complex geometries that are either difficult or too costly to produce with traditional methods like machining. For instance, creating a heavy-duty industrial valve or pump housing from a solid block of metal would be both time-consuming and expensive. Custom casting, however, allows manufacturers to produce these parts with intricate shapes and features (like internal cooling channels) with minimal waste.
The ability to create these complex shapes in a single step means that fewer secondary operations are required, such as machining or welding, which saves both time and money. Sand casting, for example, is a cost-effective way to produce medium to large-volume parts for industrial machinery. In fact, custom cast parts are commonly used in everything from automotive parts to factory machinery to high-end electronics.
Robust Parts for Heavy-Duty Applications
For manufacturers involved in heavy industries like mining, construction, and oil & gas, custom cast parts are vital for ensuring the durability and reliability of their equipment. Custom castings can be made from high-strength alloys such as carbon steel, ductile iron, and cast iron, which are ideal for the demanding conditions found in these sectors. For example, the parts used in mining machinery, such as crushers and mill linings, need to withstand extreme wear and tear.
Casting also provides a cost-effective way to produce large, heavy-duty components that would be difficult to fabricate with other methods. Parts like engine blocks, heavy machinery gears, and pumps are all commonly produced using custom casting methods because of the ability to create these components with high strength and resistance to wear without breaking the bank.
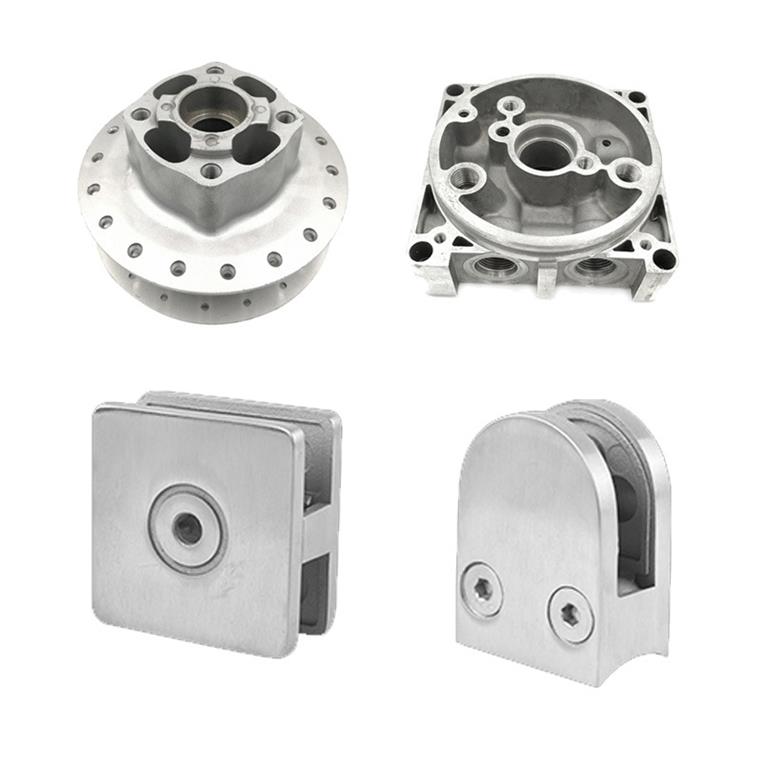
4. Energy Industry: Durability and High Performance
The energy sector is yet another industry that benefits greatly from custom cast parts, particularly in power generation and renewable energy systems. Parts in these applications must be able to withstand extreme temperatures, pressures, and environmental conditions, and custom castings are often the most reliable and cost-effective solution for this purpose.
Components for Power Generation
In traditional power plants, custom cast parts are used in turbines, compressors, and heat exchangers. These components operate under high temperatures and pressures, making durability a top priority. Cast alloys such as nickel and chromium are commonly used in these applications for their ability to withstand extreme heat and resist corrosion. Custom casting allows for the production of highly complex components with the necessary durability and strength required for efficient power generation.
Renewable Energy Components
The rise of renewable energy has also driven demand for custom cast parts. Wind turbines, for example, require large, precisely manufactured cast components, such as gearboxes and rotor hubs. The casting process is particularly beneficial in producing parts for wind turbines because it allows for the creation of large and complex components that are both strong and lightweight, which is critical for efficient energy production.
Similarly, in solar power systems, custom castings can be used to produce brackets, housings, and other structural components that need to endure harsh outdoor conditions. Custom casting is also finding applications in geothermal and hydropower, where durable parts are essential for the operation of pumps, valves, and turbines.
5. Railroad Industry: Strength and Safety
The railroad industry relies on custom cast parts to produce high-strength, durable components for locomotives and railcars. Custom castings are ideal for producing parts like wheel hubs, brake components, and track fittings, all of which must be able to withstand the stresses and strains of long-term use under heavy loads.
The strength and durability of custom cast parts make them particularly suitable for critical components in the railroad industry, where safety and reliability are paramount. Cast iron, ductile iron, and steel alloys are commonly used to produce parts that can handle the immense forces exerted on them during train operations.
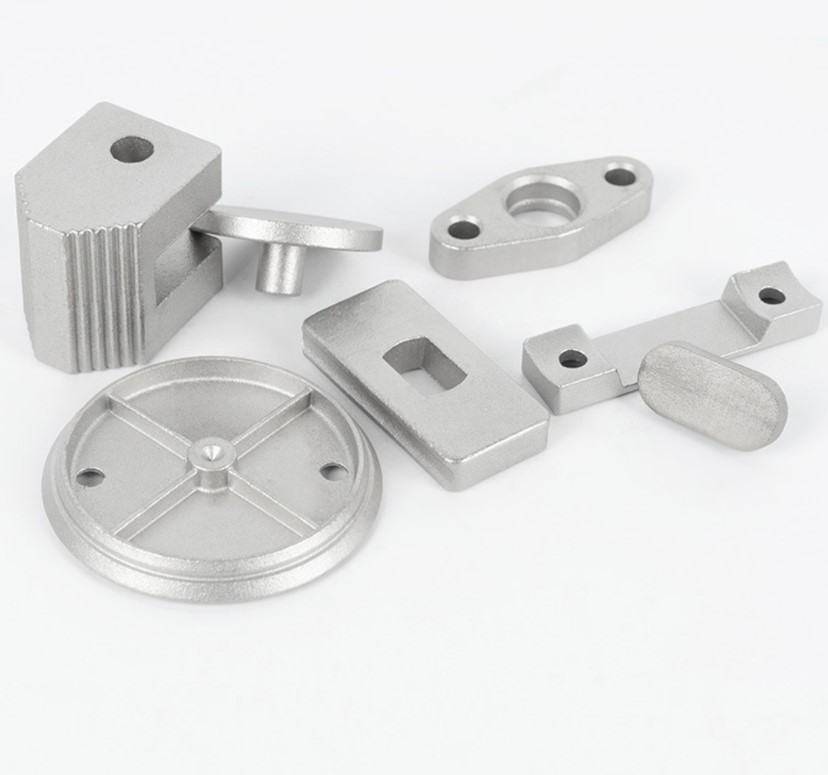
Conclusion
From automotive to aerospace to manufacturing, custom cast parts play an essential role in producing high-performance, durable, and cost-effective components across a wide variety of industries. The benefits of custom casting—such as lower tooling costs, the ability to produce complex geometries, and the versatility to work with a wide range of materials—make it an attractive option for companies looking to enhance product quality and reduce manufacturing costs.
Having worked with businesses across these industries, I can confidently say that custom casting is a crucial tool in the manufacturing toolkit, and its importance will only continue to grow as industries evolve and demand more innovative, high-quality parts. Whether you’re in the automotive, aerospace, manufacturing, or energy sectors, custom cast parts are a smart choice for delivering parts that are cost-efficient, reliable, and high-performing. If you’re considering custom cast parts for your next project, it’s worth speaking with experts in the field to find the best solutions for your specific needs.